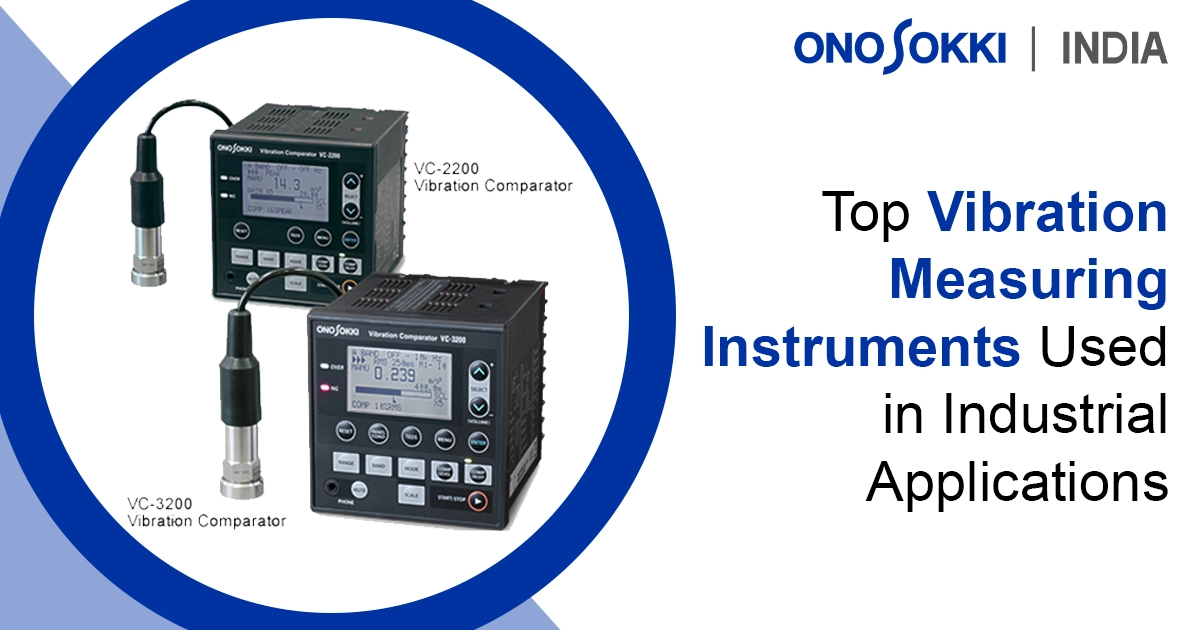
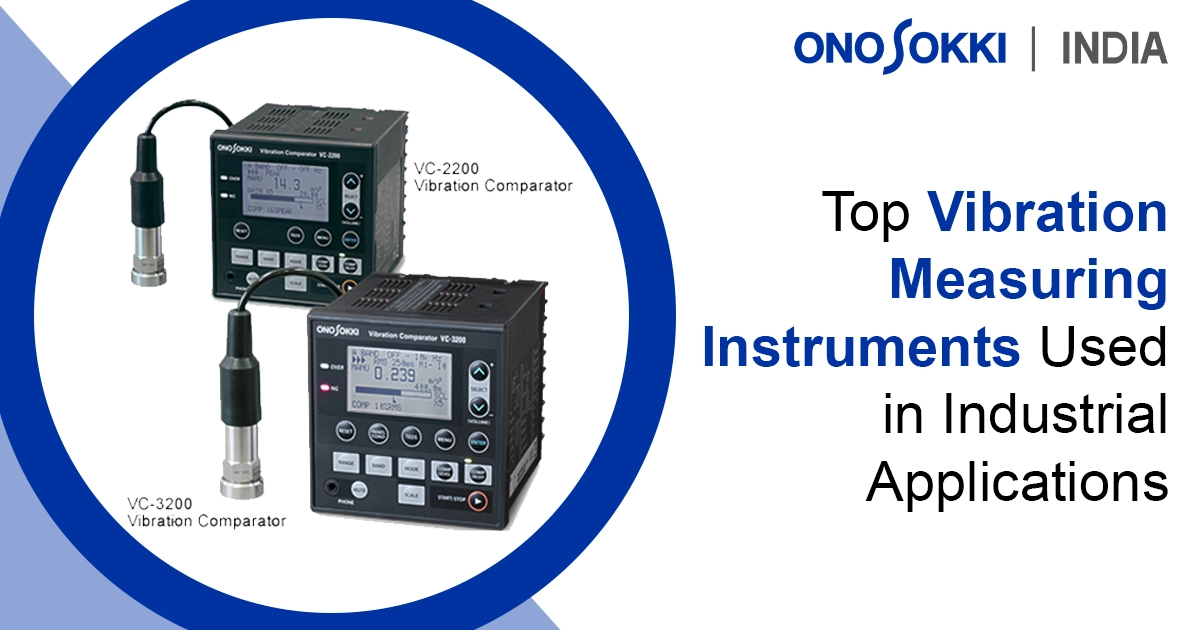
In industrial environments, machines don’t rest. Day in and day out, they operate at full capacity — and any sudden breakdown can throw the entire system off track. That’s why monitoring machine health is no longer optional. It’s essential.
One of the most reliable ways to keep machines in check is by measuring how they vibrate. That’s where vibration measuring instruments come in.
These tools help you detect signs of wear, imbalance, or misalignment early — well before they turn into costly failures. In this post, we’ll break down the most widely used types of vibration measuring instruments, what they’re used for, and how to choose the right one for your operations.
Every machine gives off a vibration signature while it runs. When things are working fine, that signature is smooth and consistent. But when something goes off — a loose bolt, misaligned shaft, or worn bearing — the vibration changes.
Spotting those changes early helps in:
In short, vibration monitoring is one of the smartest moves you can make for your maintenance strategy.
Vibration measuring instruments are tools used to detect and analyze vibrations in machinery. They pick up signals from rotating or moving parts and turn that information into data engineers can use to make informed decisions.
You’ll find these tools used across industries — from manufacturing floors and power plants to aerospace facilities and oil rigs.
They’re not all built the same, though. Some are simple handheld devices for quick checks. Others are high-end sensors that continuously monitor critical machines.
Let’s explore the different types.
There’s no one-size-fits-all tool when it comes to vibration measurement. The right instrument depends on what you’re monitoring, how often, and how precise the data needs to be.
Here are the most commonly used types:
These are the go-to sensors in most industrial setups. Accelerometers measure vibration in terms of acceleration (usually in m/s² or g-force). They’re perfect for spotting high-speed faults.
Where they shine:
Bonus: Available in single-axis and tri-axis versions depending on your setup.
Velocity sensors measure how fast an object vibrates. They’re commonly used for general-purpose industrial machines and offer a great balance between sensitivity and stability.
Best for:
These sensors don’t even need to touch the machine. Proximity probes (also called eddy current sensors) measure the gap between the rotating shaft and its housing.
Ideal for:
They give you a clear picture of how a shaft is behaving while in motion — which can help catch alignment issues early.
Displacement sensors focus on how far a component moves during vibration. They’re sensitive to changes and great for slow-moving machines.
Use them for:
If precision is key, displacement sensors are the right call.
Need a quick on-the-spot reading? Handheld vibration meters and analyzers are great for that. They’re easy to use, portable, and give you instant results.
Perfect for:
Many models also store past readings so you can compare trends over time.
In modern plants, everything is going smart — and vibration sensors are no exception. Wireless sensors collect data in real time and send it straight to your computer or cloud dashboard.
Why use them:
Use case: Monitoring machines in hard-to-reach areas like rooftops, offshore rigs, or remote facilities.
Data loggers track vibration over extended periods. Unlike instant-read devices, they’re built for long-term monitoring and are often used during testing or product transport.
Great for:
With so many options, how do you know which one’s right?
Here are a few things to consider:
Each plant has its own needs. The key is choosing a solution that fits your workflow without overcomplicating it.
Even the best sensor won’t help if it’s not used right. Here are a few tips to get more value from your setup:
Vibration monitoring works best when it’s part of a larger condition-based maintenance strategy.
Vibration monitoring is evolving fast. AI and IoT are taking over routine inspections. Today’s sensors don’t just record — they analyze, alert, and even predict.
Imagine getting a notification on your phone before a motor starts failing. That’s no longer a futuristic idea. It’s happening now with cloud-based platforms and smart industrial sensors.
The next step? Fully automated maintenance that takes human guesswork out of the equation.
Choosing the right vibration measuring instruments can make all the difference in keeping your machinery healthy and your operations smooth.
Whether you’re doing quick field inspections or setting up a full-blown monitoring system, understanding the types of vibration measuring instruments and how to use them is a huge advantage.
Start small if needed — even basic tools can help you catch issues early. And as your operation grows, you can scale up to smarter, more connected solutions.